Companies spend a lot of time and money to keep employees and assets safe in their warehousing operations, but one problem that can be difficult to address is protecting forklift loads. Although forklifts are a primary cause of damage to loads and pallets, many companies passively accept these losses as the cost of doing business. With the direct loss from stock damage and the knock-on effect of extended warehouse downtime, it makes sense to minimize damage to products and other equipment. So what can be done to reduce damage inflicted during the loading and unloading of pallet-loaded goods and while they are on the move?
Leading Causes of Goods Damage by Forklifts
The most common causes of damage to forklift loads can be summarized as follows:
-
Puncturing the load when forks aren’t correctly aligned with the pallet. If this happens, the blades of the forklift can puncture or crush the product. The forks could also disrupt the load and push it off the pallet.
-
Crushing the load when it is loaded on the forks with too much force. The hard knock against the shank can damage the pallet or the load contents.
-
Slipping off the forks usually happens when the forklift works in wet or cold areas. Dropping off the forks is especially dangerous because the falling load could hurt the operator or a nearby worker.
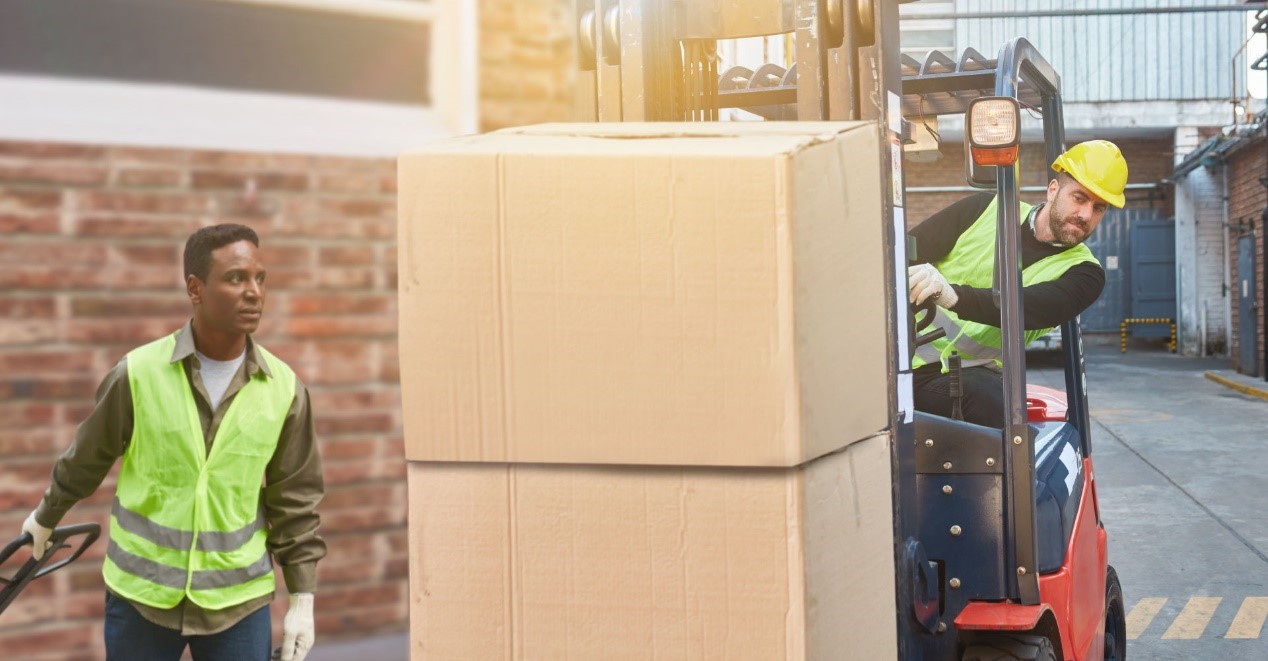
General Safety Measures for Protecting Forklift Loads
Currently, several safety measures can protect forklifts, drivers, and inventory in the warehouse.
Training and education
General operator training is not always sufficient and often fails to train drivers to handle pallets and loads with care, leading to carelessness and damaged goods. Even with proper training, when the warehouse is busy and drivers are in a rush, they may enter the pallets too quickly and misjudge the load.
Safe warehouse setup
This entails correct picking operations setup and storing all loads and pallets correctly. Another aspect is leaving aisles wide enough for unhindered operation of the forklift.
Good load setup
If a load is not stacked correctly on the pallet, it will likely fall over. The entire load should have enough wrapping to keep it in place, and it should be balanced and squared on the pallet.
Plastic pallets
Although three times the price of wood pallets and accounting for only 5% of all pallets, plastic pallets offer some compelling advantages. They allow for a full deck without gaps to fall through, are more durable than wood, create less debris in the warehouse, and offer efficient design elements like chamfered edges for better fork entrance.
Bumpers and guards
These softer rubberized sleeves cover parts of the fork to soften the blow or the forklift against the load. Three popular options are: fork back covers for the shank area, anti-slip covers that fit onto the fork blades, and soft fork blade caps for the sharp fork ends.
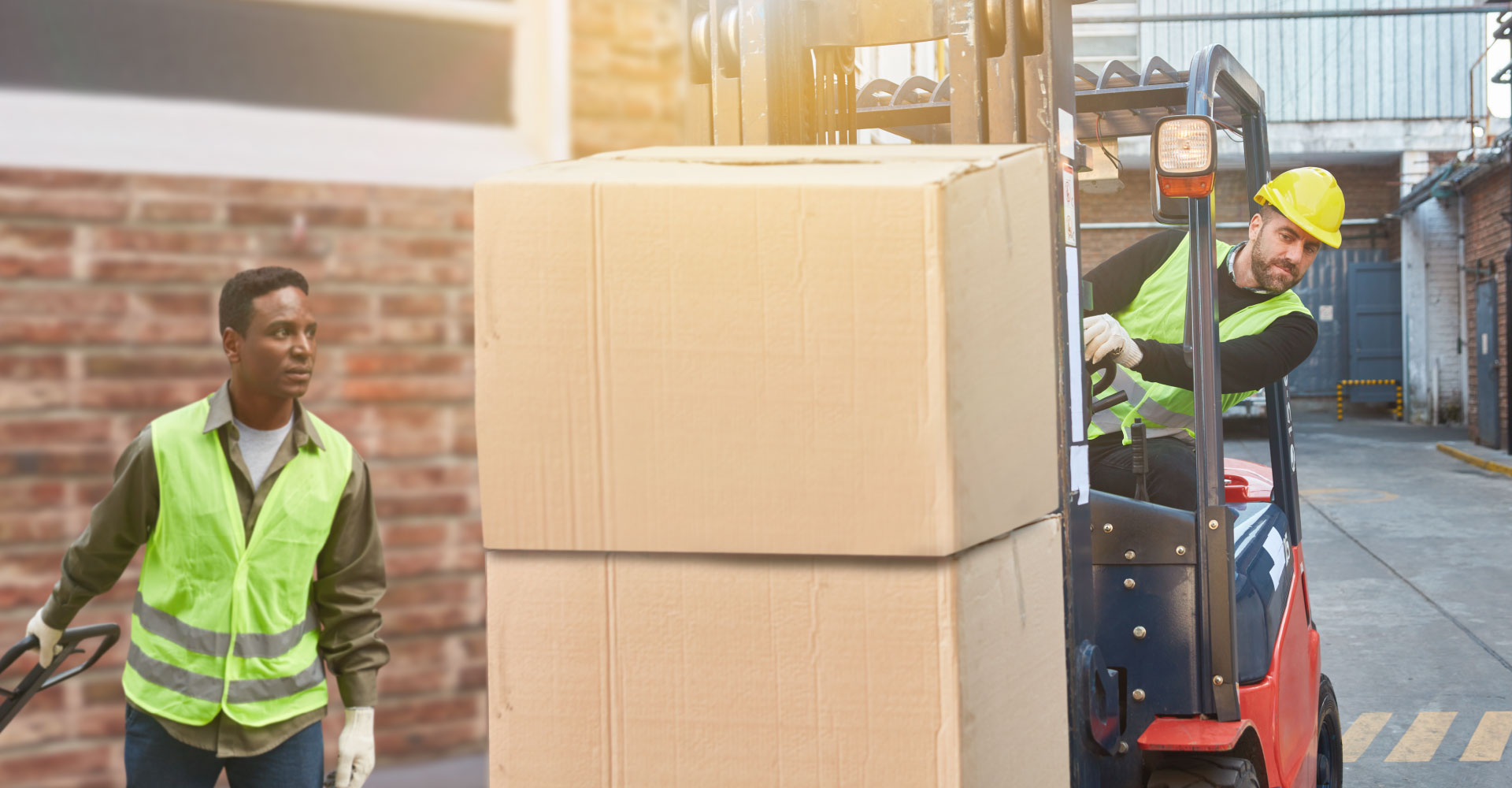
Future Developments for Protecting Forklift Loads
Technology-driven safety solutions can provide greater insight into potential risks and take some of the pressure off operators through the automated enforcement of safety protocols.
Fork camera
Although not a new technology, a camera placed between the forks close to the driver (at the fork heel) provides a view of the fork angle into the pallet. This allows for far greater accuracy, especially with the large distance and wide angle when loading and unloading at higher levels.
Mid-mast camera
This camera position provides a view just below the forks when in an upright position. The advantage of this position is that it can provide a good viewing angle for getting the load into place when placing the load. Again, this simply provides a better view of lifting action high in the air that would otherwise necessitate the driver tilting their head at an uncomfortable angle to get a decent view.
Telemetrics analysis
With the steady rollout of cloud-based data collection systems, there is much potential to reduce fork load damage through deeper analysis of the relevant data. Sometimes, the easiest way to get improvement is to incentivize and encourage current operators to do better. Data empowers this. An objective calculation of performance can be made by correlating time-at-work, time-in-seat, pallets moved, and accident events. That data will indicate which warehouses are operating more efficiently and allow a deeper analysis of which employees are working at their best and those lagging. In either case, managers can reward those who do well or take action against those who continually underperform.
Conclusion
Current approaches to protecting forklift loads go a long way to ensuring inventory gets to where it needs to go in one piece. Cloud-based management and data analysis can supplement current techniques to provide more comprehensive protection against warehouse incidents. With modern telemetrics, companies are already increasing their throughput and making sure more of their products reach their customers in prime condition every time.